Features
- Warehouse management: reception, location, supply and expedition processes.
- Customer management: full management of customer information necessary for order management.
- Customer information regarding production and delivery addresses.
- Specific conditions for packaging and palletizing by customer.
- Guidelines for order preparation and shipping requirements.
- Integration with ERP for customer management. Expedition management.
- Preparation of customer orders. Systems in sequence, Kanban, Pokayokes.
- Reports
We work on 3 pillars
Visibility
All members of the supply chain see the real state of the rest of the actors.
Infrastructure
The use of technology and process engineering allows actors an immediate response to fluctuations in demand and possible unforeseen events.
Coordination
By sharing information and making decisions, it ensures that the actors work in an aligned way and with possible unforeseen events.
Why implement
the WHALES system?
Control
All movements are recorded at the time they are made, so all information is available online. Online stock control: registration of entries, exits and regularizations. Online movement control: each operator carries out the movements with their user who is registered in the system. Total online traceability: all movements in the system can be traced 100%.
Integration
By integrating with clients and suppliers, it eliminates manually entering data into the system.
Information flow between terminals
All terminals are connected in the warehouse, which allows all the information to be available online.
Productivity
The system guides operators by generating tasks, which reduces downtime.
Optimization
By parameterizing the system, both the warehouse space and the routes in the generation of routes are optimized.
Dashboard
Having all the information on stocks, movements, traceability and incidents online allows you to make decisions in time.
Cost reduction
All these points allow for cost reduction, increasing companies' profits.
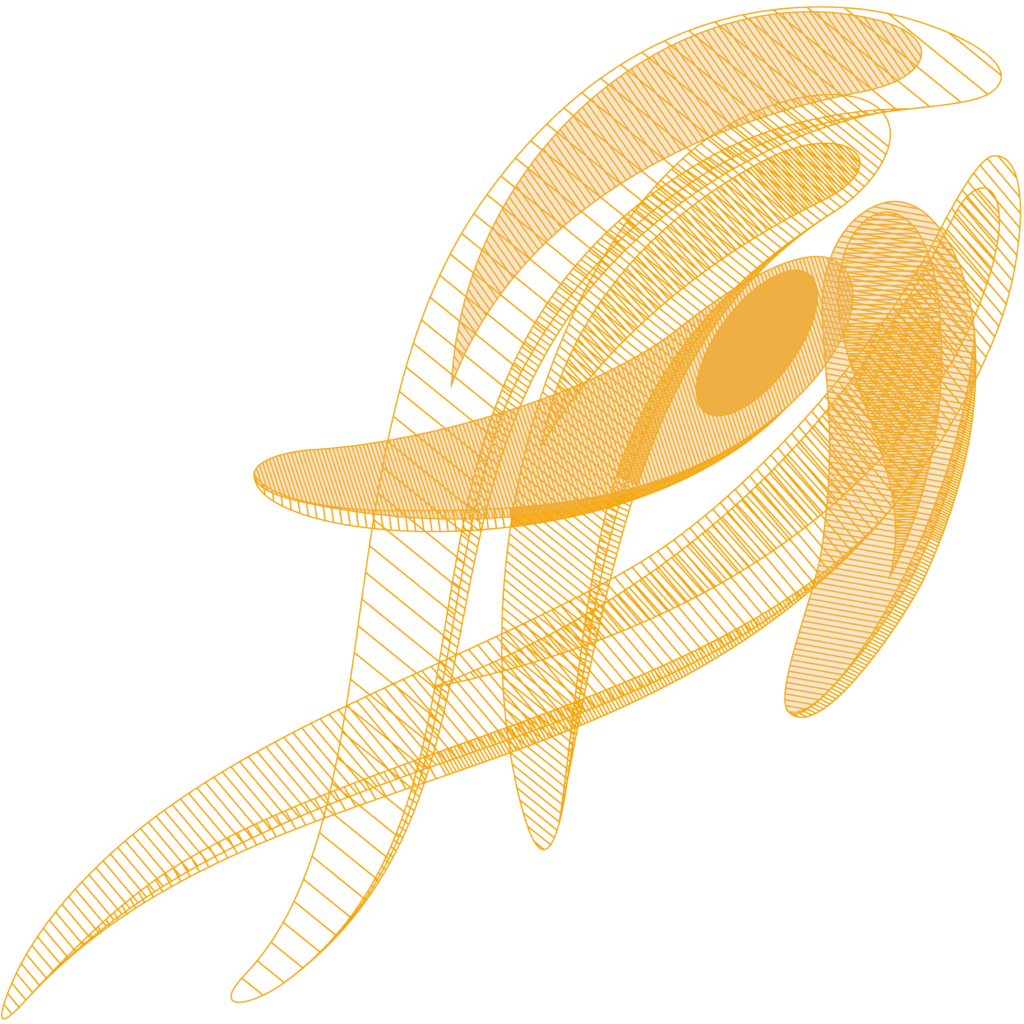